Scrap Free Beverage and Food Can Process Line Increases Production Rates by 5X While Decreasing Costs
THE CUSTOMER STORY
Polytech America LLC, a film and sheet-metal lamination company that uses its industry-leading technology to produce traditional and easy-open food, soda, and aerosol cans, was relocating from Florida to Canton, Ohio, to gain a more powerful regional presence in its highest distribution area.
The relocation to a new production facility presented an opportunity for the company to improve its existing process line that showcases its proprietary metal adhesion and polymer technologies. The company partnered with Machine Concepts to innovate and build a new high-speed process line.
THE CHALLENGE
When Polytech America turned to Machine Concepts, they asked our engineers to design a custom, high-speed solution to produce scrap-free coils of their patented PolyKote product.
During production, the start of every coil inevitably produces unusable product until the lamination process comes into phase. In the past, this material would be wound with prime material and delivered to the end-user as part of the delivered coil. The amount of usable product would vary pending the quality conditions at start-up, which resulted in the end user being forced to deal with unsellable scrap.
THE MACHINE CONCEPTS SOLUTION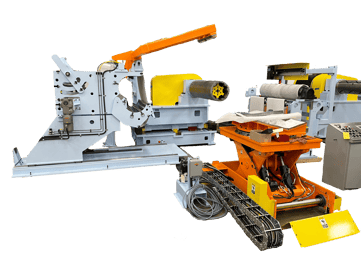
To produce scrap-free coils, the solution needed to include custom equipment to thread and wrap the sellable material received from a scrap shearing process. Maintaining an accelerated line speed, scrap material would be discarded through a shearing process until achieving quality product. At that moment, the system would transition to high-speed threading and wrapping while maintaining a line speed critical to the lamination process. The rewind unit then would continue to build the coil while maintaining accurate tension and edge control.
The goal was for higher production rates, a decrease in waste material costs, and greater overall efficiency while producing scrap-free sellable product.
THE RESULTS
Machine Concepts designed and built a process line that runs 5X more efficiently than its previous line and produces scrap-free coils.
Conventional equipment was redesigned to integrate custom thread conveyor and belt wrapper technologies to meet customer speed specifications. The previous line threading at 30 foot per minute, would now thread at 200 foot per minute.
All of this, including improvements in tension control, edge guide technology and more efficient coil handling on the entry and exit end provided Polytech with the tools to deliver higher quality, scrap free coil and increase value delivered to its customers
THE STACKING SYSTEM’S KEY TECHNOLOGIES
- Entry Scissors Lift Coil Car with Coil Rotate
- VFD Motor-Driven Unwind
- Hydraulic Expanding Serpentine Unwind Mandrel
- Exit Deflector Stand with Pivoting Thread Conveyor
- VFD Motor-Driven Rewind with Integral Hold Down
- Rewind Fitted with Automatic Proportional Hydraulic
- Lateral Adjust Edge Guide System
- Hydraulic Expanding Full-face Rewind Mandrel for Thin
- Gauge Material
- High-Speed Belt Wrapper with Cinch Wrap Technology
- Exit Scissors Lift Coil Car with Coil Rotate
- Integrated Hydraulic Power System
- Integrated Controls Package with Taper Tension Control
At Machine Concepts, we design and build a wide range of coil processing terminal equipment. With extensive experience in both mill and service center applications, we can engineer innovative solutions for the most demanding requirements
For more information, contact Machine Concepts: 419-628-3498 / machineconcepts.com/contact.