Press-to-Press Transfer System Reduces Labor and Increases Production
THE CUSTOMER CHALLENGE
An industry-leading press and automation company that had partnered with Machine Concepts on previous projects reached out in need of a fully automated, press-to-press transfer system as part of a stamping solution they were building for a customer.
While replacing old stamping presses as part of a line upgrade, the customer requested a solution that would remove the manual labor between each press. With labor shortages and several safety protocols in place, the manual transfer between presses was highly inefficient and costly.
The press and automation company turned to Machine Concepts as a trusted partner to engineer a one-of-a-kind, automated multi-press transfer system that could achieve optimal production numbers.
THE MACHINE CONCEPTS SOLUTION
Machine Concepts custom designed and built a fully automated, multi press-to-press transfer system to transfer parts from one press to another automatically. The solution includes a high-quality vacuum system so no parts are lost in the transfer that can easily be changed out to an electromagnet part pickup system.
How It Works:
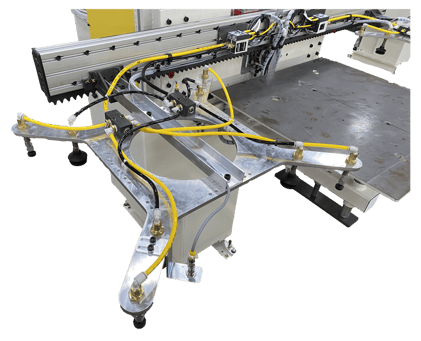
- The first press will stamp out the first progression of a part from the strip. Once the press completes its cycle, it will let press transfer #1 know it is ok to enter the die and pick up the part.
- The transfer beam has end of arm tooling at each end of the transfer beam and will move into the die via rack n pinion driven by a servo motor until it is over the part. The transfer beam will move down via ball screw and servo motor until the end of arm tooling #1 is touching the part. Once the end of arm tooling is touching the part, the vacuum system will turn on and grip the part. Then the transfer beam will raise and move to a table at the center of the transfer. It lowers the part onto the table, releases the part, raises and returns to its home position. Once at the home position, it will tell the press that the transfer is clear and the press can stamp the next part.
- When the press is done stamping the part, the press transfer will enter the die and pick up the part. While it is picking up the part in the die, end of arm tooling #2 will pick up the part on the table at the same time. The press transfer now has two parts.
- The transfer beam will then move so that end of arm tooling #1 is over the center table and end ofarm tooling #2 is inside the die of press #2. The transfer beam will lower the parts on the table andin the die at the same time, release the part, raise and move to the home position, letting the press know it is clear and can stamp. There is a part now in press #1 and press #2.
- This sequence will continue until the part has made it through all four dies. On the last station, instead of placing the part in a die, the press transfer will place the part on a conveyor system to be stacked in a box.
To provide flexibility that could boost productivity even further, the transfer system was designed with a central controller that could communicate individually to each transfer station. The customer now has the capabilities to have one press idle while the others run or to run multiple parts within the line.
KEY TECHNOLOGIES
- Actuator for a mechanical arm
- Rolling racking pin to achieve higher velocity and accuracy
- Selection of linear guide rails and roller rack and pinion for longevity of components
- High-quality vacuum system, mechanical gripper or electromagnet end-of-arm tooling
- Optional servo rotation to flip the part over
THE RESULTS
The new automated, press-to-press transfer system provided a 20% increase in production capacity. It also eliminated the manual labor of four people between the presses. The line now only needs an operator at the beginning and an operator at the finish.
Whether you’re looking for individual components, completely automated turnkey press production lines or custom designed equipment such as scroll lines, stacking and transfer systems, our team of experts can meet your needs. We are known globally for robust press room equipment that doesn’t fail.
Transform Your Challenges into Opportunities with a Machine Concepts Solution. Download the full case study below.