Overcoming Crossbow and Extreme Edge Wave Defects in Manufacturing: A Comprehensive Guide
In the world of manufacturing, quality control is of the utmost importance. Defects in the production process can lead to increased costs, delays and unsatisfied customers. Among the most common and troublesome defects are crossbow and extreme edge wave shape defects, which can have a significant impact on the overall quality and functionality of the end product.
In this blog article, we will delve into the causes of these shape defects in coil processing and discuss effective shape correction leveling solutions.
Understanding Crossbow and Extreme Edge Wave Defects
Crossbow defects occur when a strip of material exhibits a curvature across its width, resembling the shape of a bow. This can lead to slitter-induced edge wave and outgoing slit width accuracy can be affected. In addition, it can create assembly difficulties and a compromised final product.
On the other hand, extreme edge wave defects are characterized by irregularities along the edges of a strip, which can cause similar issues in the downstream process.
“Crossbow and extreme edge wave are the most challenging shape defects to remove because these types of defects strain the leveler more than other shape defects, such as coil set,” says Chris Heid, an engineer and Leveler Product Manager at Machine Concepts. “Both defects are commonly observed in the metal processing and rolling industries, but they can be overcome with the right shape correction leveling solution in place.”
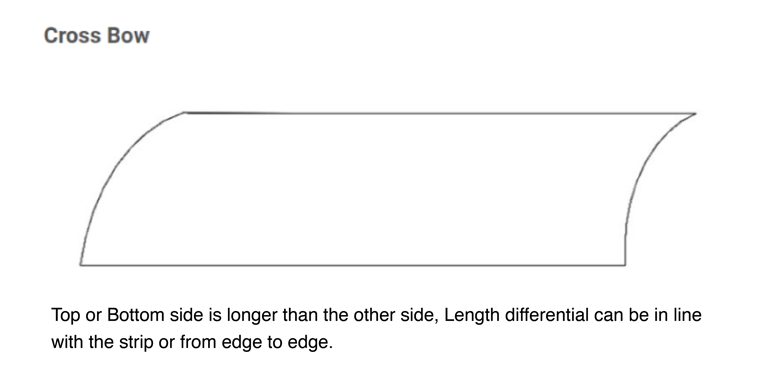
>>> Get more education and training on shape defects.
Causes of Crossbow and Extreme Edge Wave Defects
Understanding the root causes of these defects is crucial for their effective mitigation. Crossbow defects typically result from uneven cooling or heating of the material, misaligned rolls and uneven roll pressure.
In contrast, extreme edge wave defects are often caused by excessive roll bending or deflection, imprecise roll alignment and uneven tension in the material during processing.
Preventing Crossbow and Extreme Edge Wave Defects
Mitigating crossbow and extreme edge wave defects requires addressing the underlying causes, such as roll deflection and misalignment.
Manufacturers should invest in advanced levelers and tension control systems that can help ensure a uniform stress distribution across the material during processing. Additionally, regular roll maintenance is vital to avoid uneven pressure and minimize the risk of shape defects.
Advanced Levelers to Mitigate Shape Defects
At Machine Concepts, our roller levelers and tension levelers can be integrated into cut-to-length lines and coil-to-coil lines. This advanced technology removes crossbow, extreme edge wave and center buckle defects, leveling the strip and improving the efficiencies of downstream processes.
Our revolutionary and patented AutoFlat® Roller Leveler reads the shape of the strip under tension and automatically adjusts roll bending to achieve and maintain a flat strip. It has been proven that shape is most accurately read under tension. Unlike other systems that use lasers, AutoFlat® is unique in that it is the only system that can truly do this on a leveler application.
“The AutoFlat® shape measurement system provides quick and understandable visual feedback to the operator that illustrates what parts of the material contain shape issues,” Heid points out. “This measurement system not only helps the company process material using operators with limited leveling knowledge, but it also serves as a training tool to teach them how to level.”
Furthermore, our levelers are also manufactured with a patented AutoSync® drive system to increase the leveler capacity and reduce the energy required for leveling.
As an engineering-based machinery builder, we custom design shape correction leveling solutions to fit your needs, including integrating them into existing process lines with limited spacing. Contact us today to learn more.